- CIPD level 5HR02 Assignment: Talent Management and Workforce Planning Unit Guide
- Level 3 D/615/3823 Assignment: Regulation, Protection, and Collaborative Practice in Health and Social Care
- PGM216D Assignment: Bicycle Store Sales Management Application
- MATH6033 Assignment: Epidemiological Investigation of Cardiovascular Health and Tea Consumption Risks
- EH6147 Assingment: Stakeholder Analysis for Quality Improvement in Hand Hygiene Compliance
- Assignment: Investigation of Solution Concentration Through Standard Preparation, Titration, and Colorimetry Techniques
- MATH6033 Assignment: Cardiovascular Risk and Tea Drinking: Epidemiological Analyses
- CIPD level 3 3CO03 Assignment: Core behaviours for people professionals
- DAC4B1: Personal development in adult care settings
- Unit 19 Research Project Assignment 1: Impact of Corporate Social Responsibility on Business Success & Community Wellness
- EG5022 Assignment: Georeferencing and Accuracy Assessment of a Quarry 3D Model Using Photogrammetric GCPs
- Assignment: Financial Performance and Strategic Analysis of a UK Listed Company: A CORE Evaluation and Reflective Review
- 5CNMN002W Assignment: Advanced measurement- Major measurement taking off
- K/650/2298 Level 3 Understanding Roles, Responsibilities, and Effective Partnerships in Health and Social Care
- Understanding Information and Knowledge Management in the Workplace: A Briefing for HR Professionals
- HRM7010D Strategic Use of People Analytics in Enhancing Organisational Value and Agility
- TOWN1060 Urban Planning in the UK History Sustainable Design and Future City Development
- OTHM Level 5: J/650/1143 Research Methods in Health and Social Care
- Feasibility Study for Night Moves: Event Logistics at Finsbury Park, Assignment 2
- EU Law: Dominant Undertakings & EU Four Freedoms – Legal Implications and Market Impact
Unit 5048 J/650/2990 Sensors and Automation BTEC Level 5
University | Pearson College London (PCL) |
Subject | Unit 5048: Sensors and Automation |
Introduction
Modern developments and applications of automation in industry rely on complex and highly reliable industrial communication networks. Industrial communication is typically a mixture of multilayered, multidimensional networks involving fieldbuses, software packages, media, and a host of other tools. To be able to install, commission, maintain and troubleshoot an industrial plant, a competent engineer requires a good understanding of sensor and actuator technologies and core communication technologies. This unit equips students with the requisite knowledge of sensors and actuators and the key skills underpinning popular industrial communication networks, such as PROFINET, Ethernet IP, Modbus, IO Link and EtherCAT, thereby extending the breadth of employment to which students pursuing a career in network technologies can aspire.
Thus, this unit aims to provide students with the skills and competencies required to work in the areas of industrial computer control, automation, and Industry 4.0. Fundamental concepts underpinning the use of sensors and industrial communication networks for automation are introduced, and students are given the essential knowledge and skills required for the use of Ethernet-based technology in support of real-time industrial network environments. An appreciation of technologies using wire pairs, fibre optics, satellites and microwave transmission will be provided.
The unit will provide specialist knowledge for work with industrial controllers (e.g. programmable logic controllers (PLCs)) in the areas of manufacturing and automation using popular network technologies such as PROFINET, together with an appreciation of security aspects in relation to network- and cloud-based solutions.
On successful completion of this unit, students will have gained knowledge and skills in the application of PLCs to industrial control, and the design, development and evaluation of Ethernet-based communication and automation systems. Through appropriate tasks and assignments, students will be exposed to good engineering practices in software engineering, and in the installation, testing and maintenance of networked automation systems.
Learning Outcomes
By the end of this unit, students will be able to:
LO1 Explore computer control in a feedback configuration
LO2 Examine different types of sensors and actuators for automation
LO3 Demonstrate design and implementation skills in programming PLC-based devices
LO4 Investigate the PROFINET standard and PROFINET operations and data analysis techniques.
Do You Need Assignment of This Question
Essential Content
LO1 Explore computer control in a feedback configuration
Types of control systems:
- Industrial control systems
- Continuous-time and discrete control
- Types of controllers – continuous, discrete and logical
- Applications of different types control systems in chosen occupation/sector (e.g., space, aeronautical, mechanical, manufacturing etc.).
Control configurations:
- Open-loop systems
- Closed-loop systems
- Feedback, feedforward and cascade loops.
Control-loop elements:
- Essential components in a control loop
- Sensors and actuators – definition and examples
- Data acquisition, roles of analogue-to-digital converter (ADC) and digital-to-analogue converter (DAC).
LO2 Examine different types of sensors and actuators for automation
Overview of measurement concepts:
- Physical process variables: static and dynamic characteristics
- Signals and noise in measurements.
Sensors for automation:
- Measurement of physical quantities: typical sensors to measure temperature, pressure, flow, speed, position, and so on
- Concepts of range, calibration, precision, reliability, limitations and appropriate use, and so on.
Actuators for automation:
- Common actuators, characteristics and uses – valves, servomotors, and so on; control and safety concepts.
LO3 Demonstrate design and implementation skills in programming PLC-based devices
Programmable logic controllers (PLCs):
- Architecture, operation, scan cycle, inputs and outputs
- CPU, input and output modules, addressing convention
- Examples of industrial application (e.g. satellite and microwave transmission, avionics systems for remote sensing, geophysical multisensor system, microsensors, electronic and optical actuation, bespoke PLC network products).
Programming for PLCs:
- Programming using IEC 61131-3 standard languages such as ladder diagrams, function block diagrams, continuous function charts, structured text and sequential function charts
- Project configuration, program organisation units (POUs), tasks
- Application development using software environments; for example, human–machine interface (HMI) design using CODESYS and Siemens S7 PLCs
- Network automation applications and related tools and platforms.
Skills and competencies:
- Industrial computer control, automation, Industry 4.0 and beyond
- Integration of automation and digital systems, and impact on organisations.
LO4 Investigate the PROFINET standard and PROFINET operations and data analysis techniques.
Industrial communication networks:
- PROFINET, Ethernet IP, Modbus, IO Link, EtherCAT and other equivalent options
- Overview of operation and maintenance: types of network maintenance, monitoring and diagnostics; evaluation and implementation of maintenance procedures; troubleshooting methodologies, tools and techniques for networks and IT infrastructure; workforce roles such as engineering technician, network engineer, systems engineer, and relevant competencies; occupational standards to meet sector demands).
Buy Answer of This Assessment & Raise Your Grades
Overview of PROFINET systems:
- Requirements of real-time control networks
- Network topologies (e.g., bus, ring, start, tree, mesh, and hybrid) used in PROFINET networks
- The PROFINET standard
- Application areas for PROFINET networks (including organisational context, PROFINET Network Engineer roles and occupational relevance, CPD).
Design and implementation of PROFINET systems:
- PROFINET system design, protocols and principles of operation
- PROFINET installation, troubleshooting (e.g., isolate, repair and escalate faults based on data) and maintenance in the context of Industry 4.0
- Use of appropriate software and hardware tools; for example, ProfiTrace, Wireshark
- Use of cloud-based systems for maintenance and analytics.
Learning Outcomes and Assessment Criteria
Recommended Resources
Note: See HN Global for guidance on additional resources.
Print Resources
- Groover, M.P. (2020) Automation, Production Systems, and Computer-Integrated Manufacturing. 5th Ed. Addison Wesley.
- Love, J. (2007) Process Automation Handbook: A Guide to Theory and Practice. Springer-Verlag.
- Popp, M. (2015) Industrial communication with PROFINET. PROFIBUS Nutzerorganisation e.V. (PNO).
- Powell, J. and Vandelinde, H. (2015) Catching the Process Fieldbus: An introduction to PROFIBUS and PROFINET. 2nd Ed. Siemens Milltronics Process Instruments.
Websites
- http://www.profibus.com PROFIBUS & PROFINET International (PI) (General reference)
- http://www.profibusgroup.com PROFIBUS.PROFINET United Kingdom ‘All about PROFIBUS, PROFINET, IO-Link and omlox in the UK’ (General reference)
- http://www.profinews.com PROFINEWS ‘PROFINET, PROFIBUS, IO-Link, and omlox news from around the world’ (General reference)
- http://www.automation.com Automation.com ‘A subsidiary of the International Society of Automation’ (General reference)
- http://www.controleng.com Control Engineering ‘Control Engineering Magazine’ (General reference)
- http://www.controlglobal.com Control (General reference)
Are You Looking for Answer of This Assignment or Essay
Journals
Note: Example journals listed below provide a broad range of articles related to unit content and those relevant for the qualification. Staff and students are encouraged to explore these journals and any other suitable journals to support the development of academic study skills, and subject specific knowledge and skills as part of unit level delivery.
Control Engineering Practice. ISSN: 0967-0661.
IET Control Theory and Applications. ISSN: 1751-8644.
If you are facing difficulty in BTEC Level 5 Unit 5048 Sensors and Automation asignment, then you have come to the right place. Our experts provide a specially designed assignment help service for students. We are here to provide a free answer list written by experts for students, which you can read to increase your study efficiency. Hurry up and get your BTEC assignment done with high quality and AI free before the deadline.
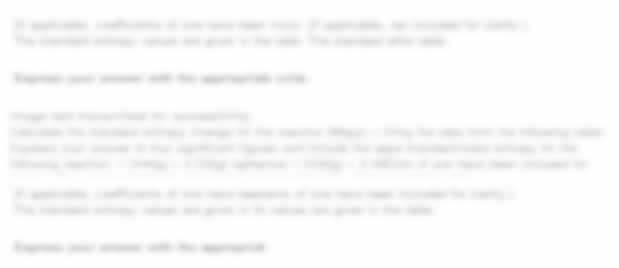